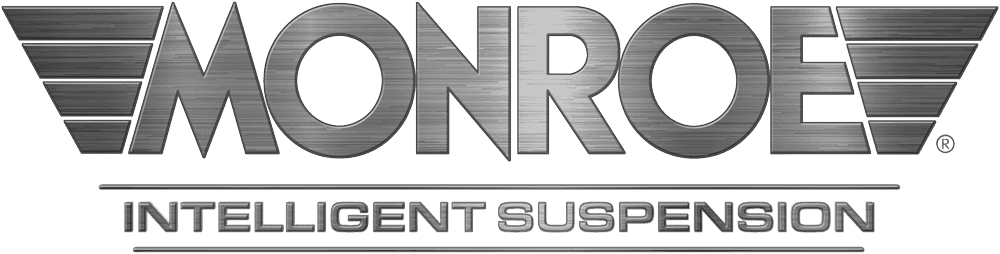
Insight is the engine of meaningful innovation
For Monroe® Intelligent Suspension, this engine combines ongoing analysis into each of the functional and emotional attributes of a superior driving experience with a clear vision of what’s necessary and possible in the years ahead.
We are a learning organization committed to helping vehicle OEMs master each leg in the journey toward the perfect ride.
Our research work focuses on 6 main areas :
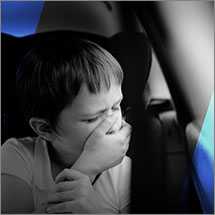
Preventing Motion Sickness in Autonomous Vehicles
Driverless cars promise increased productivity, reduced traffic congestion and fewer accidents. But one leading challenge remains: the comparatively high incidence of motion sickness experienced by passengers. DRiV and Monroe Intelligent Suspension are tackling this issue in collaboration with a leading university and other research partners.
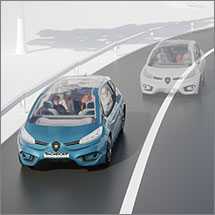
Tyre Force Vectoring:
A new frontier in ride control
The advent of electric vehicles equipped with wheel-specific motors has opened the door to individual wheel-torque control strategies that can dramatically improve vehicle dynamics for enhanced active safety, occupant comfort and powertrain energy efficiency. Learn more about this new exciting frontier in ride control.
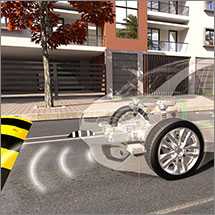
Pursuing the First Comprehensive Environment Perception System
DRiV Ride Performance engineers are exploring exciting new innovation pathways, including development of a comprehensive environment perception system offering proactive control of a vehicle’s suspension. Read more about DRiV’s “Vision” concept, leveraging laser triangulation, LiDAR, radar, stereo vision and ultrasound sensors for superior robustness and world-class driving performance.
EU Projects/University Collaboration
EVC1000 :
Electric Vehicle Components for 1000 KM Daily Trips
The project brings together ten participants from industrial and academic backgrounds to provide innovative and mass-production optimised components enabling the efficient integration of powertrain and chassis systems, which will increase EV range and user acceptance. Given the recent progress related to in-wheel motors technology, and the benefits of in-wheel architectures in terms of active safety, packaging and drivability, EVC1000 will focus on in-wheel drivetrain layouts, as well as a wheel-centric integrated propulsion system and EV manager. More specifically, the consortium will develop: - New components for in-wheel powertrains: i) Efficient, scalable, reliable, low-cost and production-ready in-wheel motors, suitable for a wide range of torque and power specifications; and ii) Dual inverters for in-wheel motor axles based on Silicon Carbide technology.
The designs will include detailed consideration and measurement of the electro-magnetic compatibility aspects, as well as the implementation of model-predictive health monitoring techniques of the electronic components. - New components for electrified chassis control with in-wheel motors: i) Brake-by-wire system for seamless brake blending, high regeneration capability and enhanced anti-lock braking system control performance; and ii) Electro-magnetic active suspension actuators, targeting increased comfort and electric vehicle efficiency.
- Controllers for the novel EVC1000 components, exploiting the benefits of functional integration, vehicle connectivity and driving automation for advanced energy management
The new EVC1000 components will be showcased in two production-ready electric vehicle demonstrators of different market segments. EVC1000 will assess the increased energy efficiency and will include demonstration of long distance daily trips. The vehicle demonstration phase will consider objective and subjective performance indicators for human factor analysis, to deliver enhanced customer experience.

This project has received funding from the European Union’s Horizon 2020 research and innovation programme under the grant agreement No 824250
XILforEV :
Connected and Shared X-in-the-loop Environment for Electric Vehicles Development
The overall goal of the XILforEV project strives for developing a complex experimental environment for designing electric vehicles and their systems, which connects test platforms and setups from different domains and situated in different geographical locations. The domains under discussion can cover (but not limited by) hardware-in-the-loop test rigs, dynamometers, material analysers, and other variants of experimental infrastructures. Real-time running of specific test scenarios simultaneously on (i) all connected platforms/devices with (ii) the same real-time models of objects and operating environments allows exploring interdependencies between various physical processes that can be hardly identified or investigated in the process of EV development.
However, the realization of connected and shared XIL experimental environment is characterized by a number of steps to be solved, e.g. communication concepts ensuring real-time capability of connected experiments, reliable methods for real-time handling of big experimental data et al. With this in mind, a strong consortium has been built, encompassing a wide spectrum of competences. In summary, the XILforEV project brings together seven complementary participants from industry and academia, to address the new design and testing tool for electric vehicles and their systems, based on a sound and objective analysis of the distributed XIL technologies, at a level of depth never attempted by any previous research on the subject. To this purpose the XILforEV activity will include novel techniques for connecting experimental labs and dedicated case studies for designing EV motion control and EV fail-safe control. In addition, considering the importance of virtual models in XIL procedures and the availability of different test benches interconnected, the proposal also addresses the development of high-confidence, real-time capable models with automatic validation using experimental data.

This project has received funding from the European Union’s Horizon 2020 research and innovation programme under the grant agreement No 824333
CLOVER :
Robust Control, State Estimation and Disturbance Compensation for Highly Dynamic Environmental Mechatronic Systems
The main goal of the CLOVER project is to offer a novel methodology in an environmental mechatronic control system design relying on multidisciplinary knowledge. This methodology should allow aspects to be taken into account, such as controller robustness, indirect measurement of system states and parameters, and disturbances attenuation on the stage of establishing controller architecture. In addition, methods for tuning the control algorithms will be developed and based on the solution of optimization task considering control priorities, such as environment friendliness and energy efficiency. The implementation of the project CLOVER is based on intensive staff exchange that will lead to collaborative research and training between universities and industrial organizations from Germany, Austria, Belgium, Norway, UK, Mexico, and Japan.
To guarantee a strong focus of the project activities on real-world problems, the CLOVER concept is based on the R&D and training in three interfacing topics: “Mechatronic chassis systems of electric vehicles”, “Mechatronic-based grid-interconnection circuitry”, and “Offshore mechatronics”, which will identify and facilitate collaborative learning and production of innovative knowledge. The CLOVER objectives will be achieved through intensive networking measures covering knowledge transfer and experience sharing between participants from academic and non-academic sectors, and professional advancement of the consortium members through intersectoral and international collaboration and secondments. In this regard, the CLOVER project is fully consistent with the targets of H2020-MSCA-RISE programme and will provide excellent opportunities for personal career development of participating staff and will lead to the creation of a strong European and international research group to create new environmental mechatronic systems.

This project has received funding from the European Union’s Horizon 2020 research and innovation programme under the grant agreement No 734832
PROCETS :
PROtective composite Coatings via Electrode position and Thermal Spraying
Wear and corrosion of materials causes losses of 3-4% of GDP in developed countries and billions of Euros are spent annually on capital replacement and control methods for wear and corrosion infrastructure. As a result many important industries are dependent on surface engineering of protective coatings, making it one of the main critical technologies underpinning the competitiveness of EU industry. There are 2 main techniques that dominate the protective coatings sector: hard chromium (HC) plating and thermal spray (TS). However, HC plating faces a series of issues with most important the extremely negative health and environmental impact leading to the EC restriction of this method for using Cr+6 by the end of 2017. Similarly, recent toxicity studies concerning Co-WC cermet applied by TP have revealed that Co-WC particles are toxic in a dose/time-dependent manner. Consequently, there is the necessity of finding new, less hazardous methods and materials exhibiting the same or better performance compared to existing ones.
The PROCETS project will take advantage of the use of nano-particles for production of composite coatings with superior properties compared to those of HC produced by electroplating or to Co-WC produced by TS. These novel nano-particles will be incorporated into existing production lines after appropriate modifications. The new procedures will be easily transferred by minor adaption to the present electroplating and TS facilities, and will combine flexibility and mass customization abilities, restrict environmental and health hazards and finally be available at acceptable cost. Thus, PROCETS main target is to deliver protective coatings covering a wide range of applications such as automotive, aerospace, metal-working, oil and gas and cutting tools industries via thermal spray and electroplating methods by utilizing more environmental friendly materials, compared to the currently used.

This project has received funding from the European Union’s Horizon 2020 research and innovation programme under the grant agreement No 686135
EVE :
Innovative Engineering of Ground Vehicles with Integrated Active Chassis Systems
Innovation technologies in ground vehicle engineering require strong interdisciplinary and intersectoral investigations with an international dimension. In this context the project EVE proposes sustainable approach based on intensive staff exchange that leads to collaborative research and training between universities and industrial organizations from Germany, Belgium, Spain, Sweden, The Netherlands, South Africa, and the USA. The project includes basic and applied research, development design, experimentations, networking, and dissemination and exploitation activities. The research objectives are focused on the development of (i) experimental tyre database that can be used in the design of new chassis control systems and subjected to inclusion into Horizon 2020 pilot on Open Research Data, (ii) advanced models of ground vehicles and automotive subsystems for real-time applications, and (iii) novel integrated chassis control methods.
It will lead to development and improvement of innovative vehicle components such as (i) an integrated chassis controller targeting simultaneous improvements in safety, energy efficiency and driving comfort, (ii) new hardware subsystems for brakes, active suspension and tyre pressure control for on-road and off-road mobility, and (iii) remote network-distributed vehicle testing technology for integrated chassis systems. The project targets will be achieved with intensive networking measures covering (i) knowledge transfer and experience sharing between participants from academic and non-academic sectors and (ii) professional advancement of the consortium members through intersectoral and international collaboration and secondments. The project EVE is fully consistent with the targets of H2020-MSCA-RISE programme and will provide excellent opportunities for personal career development of staff and will lead to creation of a strong European and international research group to create new hi-tech ground vehicle systems.

This project has received funding from the European Union’s Horizon 2020 research and innovation programme under the grant agreement No 645736
CREMA :
Cloud-based Rapid Elastic Manufacturing
Due to the proliferation of ICT Technologies, manufacturing industry is undergoing substantial transformation in terms of HW but also in terms of Cyber-Physical Production Systems and the SW and services used within production environments. In parallel, the manufacturing processes of the future are changing and need to be highly flexible and dynamic in order to satisfy customer demands for, e.g. large series production, mass customization, or changing orders.
To keep pace with the needs of the manufacturing industry of the future, in Manufacturing 4.0 companies need to flexibly react to these demands and be able to offer production capacities in a rapid way. Thus companies looking for manufacturing capacity need to be supported by the means to find these capacities, configure them, and integrate them into their own manufacturing processes.
To achieve this, one obvious approach is to port successful concepts from the field of Everything-as-a-Service (XaaS) and Cloud computing to manufacturing to mirror agile collaboration through flexible and scalable manufacturing processes:
- Leasing and releasing manufacturing assets in an on-demand, utility-like fashion
- Rapid elasticity through scaling leased assets up and down if necessary
- Pay-per-use through metered service
Applying these principles, Cloud manufacturing can move manufacturing processes from production-oriented to service-oriented networks by modelling single manufacturing assets as services in a similar way as SaaS or PaaS solutions. By modelling all process steps and manufacturing assets as services it is possible to realize cross-organization manufacturing orchestrations and integrate distributed resources and ultimately manufacture products more efficiently.
While the theoretical foundations for Cloud manufacturing are manifest there are no proven tools and technologies exist in the market - CREMA aims to change this fact by providing Cloud-based Rapid Elastic Manufacturing based on SaaS and Cloud model

This project has received funding from the European Union’s Horizon 2020 research and innovation programme under the grant agreement No 637066
MetalMorphosis :
Optimization of Joining Processes for New Automotive Metal-Composite Hybrid Parts
The MetalMorphosis aims to develop a new range of novel metal-composite hybrid products for the automotive industry, based on the knowledge transfer from the Electromagnetic Forming (EMF) usage in joining dissimilar metal products and taking advantage of new developed composites and its capability to be bonded to metal.
MetalMorphosis approach is to combine and involve all the main players – Top-down and bottom-up in the value chain – from the automotive industry in the development of the next generation of metal-composites hybrid materials, ensuring a strong contribution from industrial drivers (towards those which are industry’s main needs in what concerns to automotive parts), an active involvement of SMEs (in the manufacturing of pilots / demonstrators), a valuable
participation from RTD’s (performing research activities in multidisciplinary key knowledge areas and defining the drive beyond the state-of-the-art) and – last, but not the least – a major role to be played by multipliers organizations who will ensure the exploitation of projects’ main results towards the automotive market and other linked sectors.
MetalMorphosis will gather a wide – but simultaneously specialized and multidisciplinary – consortium composed by 9 European partners, according to their expertise areas – Welding and joining technologies, Composites, Industrial Manufacturing and Automotive OEM – which have strong interest in developing new joining processes for metal-composites and lightweight materials addressing the challenges for the automotive industry for the following 10 years.

This project has received funding from the European Union’s Horizon 2020 research and innovation programme under the grant agreement No 609039
3CCar :
Integrated Components for Complexity Control in Affordable Electrified Cars
The 3Ccar project will provide highly integrated ECS Components for Complexity Control in thereby affordable electrified cars. The new semiconductors for Complexity management (Control, reduction) will offer the next level of energy efficiency in transportation systems.
3Ccar’s impact is maximizing pragmatic strategy: Use semiconductor technology innovations to manage functionality & complexity increase. This leads also to cheaper, efficient, robust, comfortable, reliable and usable automotive systems. This strengthens Europe as a whole (OEM, Tier1, Semiconductor) generating economic growth and new jobs in Europe.
The impact of 3Ccar is driven vertically by innovations and horizontally enabling growth and deployment in the industry based on what we see as European Values. We recognized that European engineers develop for highest efficiency, convergence and manageable complexity. Our society appreciates long life products to avoid waste. 50 partners and 55 Mio€ budget give the mass for
innovative products such as functional integrated powertrains, smart battery cells with unique selling features allowing Europe to advance to global leadership. An important feature of the project has been the recognition and exploitation of synergies with other EV projects, enabling fast innovation cycles between such aligned projects.
The technologies developed in 3Ccar will be commercialized all over the world while giving advantages to Europe’s OEMs willing to manufacture in Europe. 3Ccar will be involved in standardization needed to ensure that large vertical supply chains can be established. The 3Ccar project shows that collaboration between industry, research institutes, governments and customers is pivotal for excellence in Europe.

This project has received funding from the European Union’s Horizon 2020 research and innovation programme under the grant agreement No 662192
AutoDrive:
Advancing Fail-Aware, Fail-Safe, and Fail-Operational Electronic Components, Systems, and Architectures for Fully Automated Driving to Make Future Mobility Safer, Affordable, and End-User Acceptable
Automated driving is a disruptive technology which opens the door to future multi-billion markets providing business opportunities to value chains in the automotive and semiconductor industry. The European industry has leading competitive strength in the development and manufacturing of highly reliable electro-mechanical systems. In order to preserve this capability Europe needs to setup European standards for high level control such as real-time computing or big data processing. In order to respond on the global challenge AutoDrive has gathered Europe’s leading semiconductor companies, suppliers, OEMs, and research institutes committed to create a pan-European eco-system, which has the critical mass to initiate standards and provides the components and subsystems for automated driving. Currently, even the most sophisticated vehicle automation technology on the road is not able to surpass human driving capabilities – especially considering context awareness in any situation.
Moreover, there is no common agreement on quantifiable dependability measures which hardware and embedded software have to achieve to allow safe automated driving for SAE Levels 3-5. AutoDrive aims for the design of (i) fail-aware (self-diagnostics), (ii) fail-safe, (iii) fail-operational (HW and SW redundancy) electronic components and systems architecture that enable the introduction of automated driving in all car categories. AutoDrive results will significantly contribute to safer and more efficient mobility. It will raise end-user acceptance and comfort by supporting drivers in highly challenging situations (active safety) as well as in regular driving situations. Combining both will reduce the number of road fatalities especially in rural scenarios and under adverse weather conditions. AutoDrive will contribute to Europe’s Vision Zero and to improved efficiency. This will sustain Leadership and even grow the market position of all AutoDrive partners.

This project has received funding from the European Union’s Horizon 2020 research and innovation programme under the grant agreement No 737469
PRYSTINE :
Programmable Systems for Intelligence in Automobiles
The ambition of PRYSTINE is to strengthen and to extend traditional core competencies of the European industry, research and universities in smart mobility and in particular the electronic component and systems and cyber-physical systems domains. PRYSTINE’s target is to realize Fail-operational Urban Surround perceptION (FUSION) which is based on robust Radar and LiDAR sensor fusion and control functions in order to enable safe automated driving in urban and rural environments. Therefore, PRYSTINE’s high-level goals are:
- Enhanced reliability and performance, reduced cost and power of FUSION components
- Dependable embedded control by co-integration of signal processing and AI approaches for FUSION
- Optimized E/E architecture enabling FUSION-based automated vehicles
- Fail-operational systems for urban and rural environments based on FUSION
PRYSTINE will deliver (a) fail-operational sensor-fusion framework on component level, (b) dependable embedded E/E architectures, and (c) safety compliant integration of Artificial Intelligence (AI) approaches for object recognition, scene understanding, and decision making within automotive applications. The resulting reference FUSION hardware/software architectures and reliable components for autonomous systems will be validated in in 22 industrial demonstrators, such as:
- Fail-operational autonomous driving platform
- An electrical and highly automated commercial truck equipped with new FUSION components (such as LiDAR, Radar, camera systems, safety controllers) for advanced perception
- Highly connected passenger car anticipating traffic situations
- Sensor fusion in human-machine interfaces for fail-operational control transition in highly automated vehicles
PRYSTINE’s well-balanced, value chain oriented consortium, is composed of 60 project partners from 14 different European and non-European countries, including leading automotive OEMs, semiconductor companies, technology partners, and research institutes.

This project has received funding from the European Union’s Horizon 2020 research and innovation programme under the grant agreement No 783190
OWHEEL :
Benchmarking of Wheel Corner Concepts Towards Optimal Comfort by Automated Driving
The project OWHEEL aims at the development and evaluation of new concepts of automotive wheel corners as crucial elements of future vehicle architecture tailored to provide an optimal comfort during automated driving. The consortium will benchmark four essentially different classes: Passive corner with specific wheel positioning; Passive composite corner; Active corner with ordinary ride dynamics control; Active corner with integrated wheel positioning control. For each proposed concept, the project will include relevant stages of development design, extensive simulation studies and experimental validation. The main goal of the OWHEEL project is to perform deep analysis and provide on its basis the recommendations for future vehicle architecture, which could ensure an optimal comfort by automated driving. In this regard, the research and innovation objectives are focused on:
- Revisiting the driving comfort criteria with their tuning to automated driving requirements and operational modes;
- Development of benchmarking criteria and corresponding analytical tool for comparison of wheel corner concepts in terms of driving comfort quality with simultaneous ensuring of required performance in terms of safety, energy-efficiency and reliability;
- Development and validation of active wheel corner concepts;
- Development and validation of passive wheel corner concepts;
- Producing practical recommendations for automotive system developers based on obtained R&D results The implementation of the project OWHEEL will be based on intensive staff exchange that leads to collaborative research and training between universities and industrial organizations from EU, Japan and South Africa. The project will also include relevant networking, dissemination and exploitation actions.

This project has received funding from the European Union’s Horizon 2020 research and innovation programme under the grant agreement No 872907